Helmut Mathes
Planoflex heißt das von der DFTA patentierte neue Flexodrucksystem, das im Wesentlichen aus einer Druckplatte mit Niedrigrelief besteht. Die Platte druckt quasi im »Vollkontakt« – wie ein Tiefdruckzylinder oder eine Offsetdruckplatte. Planoflex revolutioniert die Flexodrucktechnik, ohne dabei echte Neuinvestitionen zu erfordern: lediglich die Druckmaschine muß für Direktantrieb und Sleevetechnologie ausgelegt sein, was ohnedies seit Jahren praktisch Standard ist. Interessant ist dabei, dass verschiedene dieser Prozeduren schon heute auf den installierten Druckmaschinen ohne Mehrkosten einsetzbar sind und die Produktion verbessern würden.
Das System wurde von Prof. Dr. Martin Dreher entwickelt und von der DFTA patentiert. Man benützt die üblichen Flexodruckplatten – aber mit einem reduzierten niedrigeren Relief – die auf den installierten Plattenbelichtern und Auswaschanlagen hergestellt werden. Die Reliefreduzierung wird durch eine längere Rückseitenbelichtung erzielt, wobei die gewählten Reliefhöhen exakt erreicht werden. Detaillierte Drucktests wurde mit Druckplatten von Flint nyloflex (jetzt XSYS), Cyrel von DuPont und Kodak Flexcel (jetzt Miraclon) auf der Zentralzylindermaschine von Fischer & Krecke (jetzt Bobst Bielefeld) im DFTA Technologiezentrum gemacht. Dabei wurden überwiegend 1,14 mm starke Platten eingesetzt. Versuche mit 0,7 mm dünnen Platten von Flint zeigten dabei keine Unterschiede – wobei dünnere Platten derzeit nicht erhältlich sind und diese trotz der geringeren Polymerbeschichtung nicht billiger wären, da die Stärkentoleranzen enger werden. Hier wären endlos-/nahtlos Sleeve ideal; aber auch hier gibt es noch einige Herstellungsprobleme. Für den Einsatz auf modernen Druckmaschinen wären lediglich ein paar Neueinstellungen erforderlich.
Die Druckabwicklung
Prof. Dreher begann seine Untersuchungen und Versuche mit dem Ziel, das Problem der Druckstreifen – wie sie im Flexo bei gewissen Motiven öfters auftauchen – zu reduzieren oder zu eliminieren. Die Versuche bestätigten, was Prof. Dreher schon länger vermutete: Alle Polymerplatten könnten ein besseres Druckergebnis ermöglichen, würde man mit einem geringen Anpressdruck der Rasterwalze zur Druckplatte arbeiten. Dies allerdings widerspräche einer alten Regel des Flexodrucks die besagt, dass – um einen gleichmässigen und satten Ausdruck zu erhalten – die Rasterwalze »scharf« angestellt werden müsse, um während des Druckvorgangs die Druckform gegen den Gegendruckzylinder zu stützen. Seine Versuche haben definitiv bewiesen, dass genau das Gegenteil richtig ist: Hoher Druck zwischen Rasterwalze und Druckplatte führt dazu, dass die Näpfchen der Rasterwalze die Druckform ziemlich rasch überfärben und die nicht druckenden Zwischenräume (Raum zwischen den einzelnen Rasterpunkten, Lettern, usw.) mit Farbe füllt. Dieses Absetzen von zu viel Farbe führt zum Zulaufen der Druckform, und damit zu Maschinenstopps für das Waschen der Druckform und zur damit verbundenen Makulatur. Zusätzlich führt diese Arbeitsweise auch zu einer erhöhten mechanischen Beanspruchung der Druckform. Die zahlreichen Druckversuche der DFTA haben bewiesen, dass zum Erreichen einer guten Druckqualität, der Beistelldruck der Rasterwalze zur Druckform niedriger sein muss, als der von der Druckform zum Druckträger (Kiss-print Einstellung). Eine falsche Druckanstellung führt zu den berüchtigten Druckquerstreifen, die bisher nur durch eine Reduzierung der Druckgeschwindigkeit eliminiert oder reduziert werden konnten; dabei kann das Entstehen von der Druckstreifen auch noch andere Ursachen haben, welche eine harmonische Druckabwicklung verhindern.
Der Flexodruck arbeitet bisher gemäß dem Prinzip des Hochdrucks mit einer Elementpressung – die Berührung der Druckform mit dem Bedruckstoff findet nur dort statt, wo die druckenden Elemente aus der nichtdruckenden Fläche herausragen. Ein Zylinderantrieb über Friktion ist daher im Flexodruck nicht möglich, weil die Druckform selten druckende Elemente über den gesamten 360 Grad Umfang hat, was die Mitnahme der Druckform durch den Bedruckstoff und den Gegendruckzylinder ermöglichen würde. Der Antrieb von Druckform- und Gegendruckzylinder erfolgte bis zur Jahrhundertwende stets über Zahnräder; und erst heute zumeist im Direktantrieb, da jeder Zylinder einen eigenen Antriebsmotor hat, der über eine elektronische Welle verbunden und gesteuert wird.
Die weichelastische Druckform
Bekanntlich wird für Flexodruck eine weichelastische Druckform eingesetzt, die einen optimalen Ausdruck auf fast allen Bedruckstoffen ermöglicht. Im Druckspalt aber – unter Druck – gibt sie nach, wodurch sich der Radius des Druckformzylinders verändert. Diese Veränderung der Druckformstärke wird durch den Unterbau der Druckform (Klebefolie) und den Undercut der Zylinder / Sleeves ausgeglichen. Beim vormaligen Zahnradantrieb der Zylinder musste die Gesamtstärke des Druckformunterbaus den Zahnrädern angepasst werden, um eine optimale Druckabwicklung zu erreichen. Die Abstufung der Drucklängen wurde durch die auswechselbaren Zahnräder – Anzahl der Zähne und deren Breite – bestimmt. Die Zahnrad-Eingriffstiefe ermöglichte Feinkorrekturen der Drucklängen.
Oberflächengeschwindigkeit
Die modernen Reihenbau-, Mehrzylinder- oder Zentralzylinder-Maschinen mit Direktantrieb und Sleeves erlauben eine individuelle Änderung der Oberflächengeschwindigkeiten (von Druckform- und Gegendruckzylinder). Die Abwicklungsgeschwindigkeiten bewirken aber – neben dem Einfluss auf die Drucklänge – auch Veränderungen in Tonwert und Druckqualität, sowie Verschleiß der Druckform. Aus Erfahrungen mit Reihenbaumaschinen weiß man seit Jahren, daß eine Verkürzung oder Verlängerung des Druckbildes (bei 60–70 L/cm Raster) von 2–3% mit dem bloßen Auge nicht erkennbar ist; bei 4–5% aber sichtbar wird. Mit Rasterweiten von 40–48 L/cm kann man bei einer Verkürzung oder Verlängerung bis 5–7% gehen. Dies ist hilfreich beim Druck von Aluminium-Folien für Yoghurt– und Kaffeemilchdeckeln, Pharma-Blisterverpackungen sowie flexible Verpackungen die vom Tiefdruck zum Flexodruck konvertiert werden; dabei werden kleinste Drucklängenveränderungen oft zum Problem.
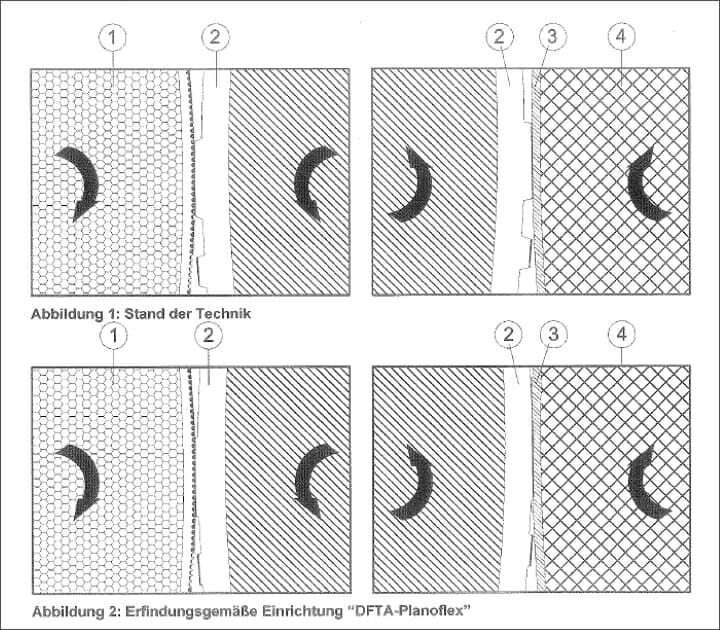
Dies könnte in Zukunft ein gewichtiger Punkt für Planoflex werden – sollten sich die Plattenhersteller entscheiden, auch dünnere Druckplatten herzustellen. Allerdings ergeben diese bei der Montage auf die vorhandenen Sleeves einen kleineren Radius (Drucklänge). Um die vorhandenen Sleeves weiter zu nutzen, könnte man alternativ ein dickeres Klebeband mit geringeren Stärketoleranzen einsetzen bzw. das Druckformat der neuen Plattenläge in der Druckvorstufe anpassen.
Bei Druckversuchen der DFTA zeigte sich als optimale Lösung, eine etwas längere Platte zu nehmen und diese verkürzt drucken (die Bahn läuft langsamer als die Druckform), da sich dabei die größeren Volltonflächen kompaktieren und voller ausdrucken. Dies ist derzeit nur eine Überlegung, da die Plattenhersteller bei dünnerer Beschichtung der Platten (Folien) mit den Extrudern an zwei Grenzen stoßen, die schwerlich zu verändern sind – das minimale Produktionsvolumen pro Minute und die maximale Laufgeschwindigkeit der Trägerfolie pro Minute; vor allem aber, weil die Stärkentoleranzen der Beschichtung bei +/– 10 µm liegen müssen. Die Wahrscheinlichkeit, dass die Industrie für Planoflex dünnere Platten produzieren wird, ist aber gleich null und genau genommen auch nicht nötig, weil die vorhandenen Plattenstärken genauso gut funktionieren.
Gleiche Plattenstärke mit Niedrigrelief
Prof. Martin Dreher machte mit seinen Studenten die Versuche im Technikum der DFTA auf der installierten Achtfarben-Zentralzylindermaschine von Fischer & Krecke (Bobst). Für die ersten Versuche wurden Fotopolymerplatten mit 150 µm Reliefhöhe eingesetzt, die bei weiteren Versuchen auf 100 µm reduzierte. Die Reliefhöhe von 100 µm zeichnet derzeit als untere Grenze ab, weil sie unter täglichen Produktionsbedingungen einfach zu erreichen ist. Die Toleranz der Reliefhöhe lag bei allen Versuchen stets bei maximal +/– 10 µm. Für alle Versuche wurden handelsübliche Platten von Flint (nyloflex), DuPont (Cyrel) und Miraclon (Kodak Flexcel) mit 1,14 mm Dicke eingesetzt. Versuche mit 0,7 mm dünnen Platten von Flint zeigten im Einsatz keine Unterschiede – weder bei der Herstellung noch im Druck. Die Druckelemente erhalten durch die Reliefhöhenreduzierung eine stärkere Versockelung durch die längere Rückseitenbelichtung. Dies hat aber auf den Druck keinen Einfluss; zudem kann man vorhandene Sleeves einsetzen, da sich die Drucklänge nicht verändert. Dünnere Druckplatten sind flexibler und mögen sich besser den Sleeves anschmiegen (was noch zu erproben wäre), machen aber nur Sinn, wenn die Platten billiger werden. Andererseits verankert ein dickerer Polymersockel feine Lichtpunkte besser und macht die Platte auch dimensionsstabiler, was bei der Plattenmontage von Vorteil ist.
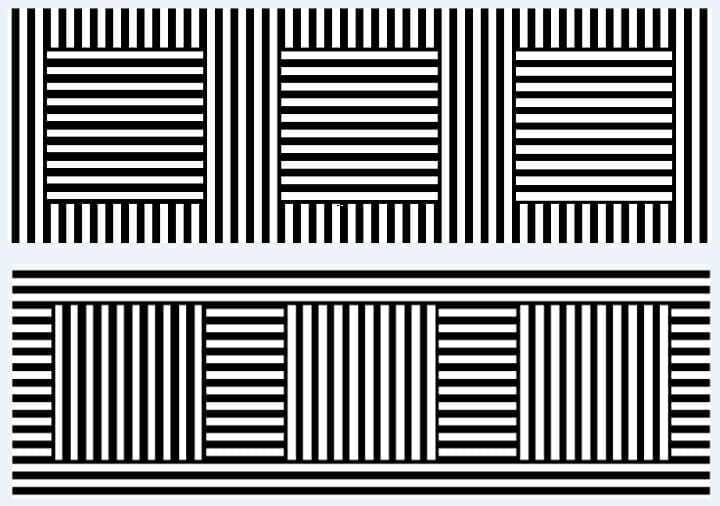
Der Anpressdruck der Druckplatte zum Gegendruckzylinder liegt bei 140 µm, der Anpressdruck der Aniloxwalze zur Druckplatte beträgt 60 µm. Daraus ergibt sich folgende Faustregel: Die Reliefhöhe der Druckplatte entspricht in etwa dem Mittelwert des Anpressdrucks von Platte zu Druckzylinder und von Platte zu Rasterwalze. Dabei muss der Anpressdruck zur Rasterwalze mindestens um die Hälfte niedriger sein als der Anpressdruck zum Druckzylinder. Diese Formel sollte man allgemein im Flexodruck einsetzen, wenn man den »Kiss Print« anstrebt. Dieser Anpressdruck garantiert eine harmonische Abrollung auch im Planoflex wo das Druckrelief knapp über dem Plattengrund liegt. Mit diesem niedrigen Reliefsockel produzieren die Anlaufkanten der Druckelemente beim Druck keine Schwingungen mehr, da Druckelement und Plattenboden beim Einlauf in den Druckspalt praktisch auf einer Ebene liegen und das Entstehen der Druckstreifen eliminieren.
Resonancenaufbau durch Druckform
Eine harmonische Druckabwicklung ist entscheidend für die Druckqualität ohne Streifenbildung die vor allem durch Vibrationen in der Druckmaschine entstehen, und durch das Hochdruckprinzip des Flexodrucks bedingt sind durch den ständigen Wechsel der Druckzustände (druckende und nicht-druckende Flächen) zwischen der Rasterwalzen, dem Druckformzylinder und dem Gegendruckzylinder mit der zu bedruckenden Bahn; dies führt zu Vibrationen die sich aufbauen und deren Ableitung in periodischen Druckstreifenschlägen auf der Bahn zu sehen sind.
Diese Vibrationen sind heute nur die Reduzierung der Druckgeschwindigkeit zu eliminieren oder zu reduzieren. Beim Planoflex-System entfällt das Reliefsystem der Druckform von druckenden und nichtdruckenden Flächen – es besteht eine praktisch uniforme Druckformhöhe wie im Offset oder Tiefdruck womit keine Resonanzen entstehen die sich aufschaukeln und periodisch entladen (siehe oben, Abbildung »Der Lösungsansatz Planoflex«)
Die Vorteile von Planoflex – bei unveränderten Plattenpreisen:
- Reduzierung der Auswaschzeiten bei der Plattenherstellung, da weniger Polymer zu entfernen ist;
- Kürzere Belichtungszeiten da die Polymerschicht dünner ist.
- Kürzere Trocknungszeiten der Platte – 30–40 min. statt 120 min.
- Geringerer Waschmittel- und Stromverbrauch
- Verdoppelter Ausstoss der Plattenherstellungsanlagen.
- Um 50% reduzierte Zeiten der Plattenherstellung.
- Geringere Verzerrungen und Verziehungen der Platte bei der Sleevemontage .
- Weniger Verzug und Deformation (Rahmenbildung) feiner Druckelemente, die isoliert in nicht-druckenden Flächen stehen.
- Bessere Passergenauigkeit der Platten zueinander.
- Kürzere Einrichtezeiten für das Farbregister.
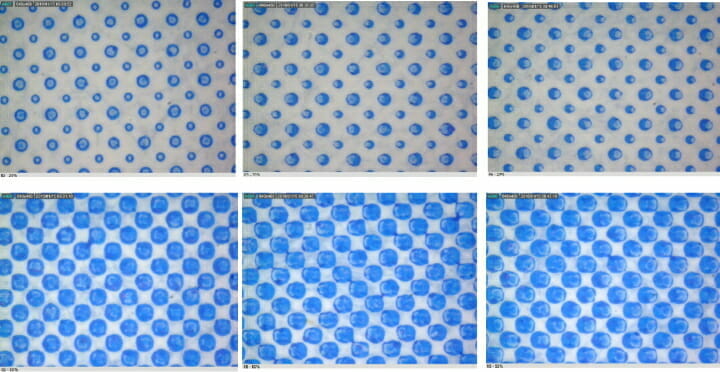
Heute setzt man im Folien-, Papier- und Kartondruck meist Platten mit einer Gesamtstärke von 1,14 mm (1140 µm) ein, mit einer Polymerschicht von etwa 0,85–0,95 mm auf einer Trägerfolie von 0,29–0,19 mm. Das bedeutet: nur etwa die Hälfte der Polymerschicht wird genutzt. Man könnte ohne große Probleme auf eine Plattenstärke von 0,4–0,5 mm gehen. Einige Druckereien arbeiten seit längerem ohne Probleme mit 0,76 mm starken Platten (0,56 mm Polymer plus 0,20 mm Folie). Allerdings reduziert dies nicht den Plattenpreis, da das jährliche Volumen zu gering ist. Von DuPont hört man, »… man habe prinzipiell kein Problem, Platten mit dünneren Schichten herzustellen die engere Toleranzen erfordern. Man benötige ein jährliches weltweites Verkaufsvolumen, das die Kosten decke und einen marktverträglichen Preis ermögliche« – was heute fragwürdig erscheint. Die Antwort von Asahi Photoproducts ist ähnlich: »… Wir brauchen ein gewisses Jahresabsatzvolumen, um eine neue Platte zu produzieren.«
Die Druckplatten für Planoflex erfordern eine Reliefhöhe von 100 bis maximal 150 µm mit einer maximalen Höhentoleranz von +/– 10 µm. Wie erwähnt, benützt man derzeit die herkömmlichen Flexodruckplatten, wobei die Reliefhöhen von 500 µm (und mehr) je nach Fotopolymersystem (flat dot oder runde Punktoberfläche) unter anderem durch eine etwas längere Rückseitenbelichtung (Bump exposure) reduziert wird – man erhöht die Versockelung der Druckelemente und lässt etwas mehr Polymer auf dem Plattengrund. Die exakte Belichtungszeit der Rückseitenbelichtung erhält man mit ein paar Testplatten; die gemessenen Höhenwerte mit +/– 10 µm werden exakt und konstant eingehalten und sind geringer als die der Rohplatten (Toleranz +/– 40 µm). Natürlich muss die Lebensdauer der Röhren periodisch kontrolliert werden.
Die engere Toleranz der Reliefhöhe ist bei Planoflex entscheidend, da die druckenden und nicht-druckenden Flächen praktisch auf einer Ebene liegen, wie bei den Druckformen des Offset (Farbe/Wasser) und Tiefdruck (Näpfchen/Rasterstege). Sie sind damit praktisch im Vollkontakt mit dem Druckträger (Bahn) kurz vor dem Eintritt in den Druckspalt. Die druckenden Elemente bei Planoflex sind durch die Reliefhöhe und den Farbauftrag um 100–150 µm höher. Dabei ist der Farbauftrag, wie im Hochdruck, das entscheidende Element und nicht der Anpressdruck. Somit werden Toleranzen von max +/–10 µm ein absolutes Muss. Dies erfordert einige kleine, spezielle Korrekturen in den Vorstufendaten. Der Einsatz von vorbeschichteten Polymer-Sleeves ist wegen der Rückseitenbelichtung derzeit nicht möglich. Der Einsatz von lasergravierten Sleeves ist allerdings noch zu prüfen. Vorbeschichtete Polymer-Sleeves sind wünschenswert, wenn verschachtelte Faltschachtelverpackungen zu drucken sind und somit Nahtlos/Endlos-Druckformen benötigt. Zudem gibt es mit vorbeschichteten Sleeves kein Problem mit Plattenabheben beim Bahnkontakt.
Die potentiellen Niedrigreliefplatten oder beschichteten Sleeves – falls sie jemals hergestellt werden – würden eine Polymerbeschichtung von 100–150 µm auf 20–25 µm starken Trägerfolien erfordern mit einem Höhenrelief von 70–80 µm und einer Gesamtplattenstärke von 190–255 µm – dies sind komplexe Vorgaben, vor allem bei einem niedrigen Absatzvolumen, da es auch mit dem bestehenden Standardpatten funktioniert.
Laut DFTA zeigten die ganzen Testreihen mit Planoflex, dass das System ohne Probleme funktioniere beim Druck auf Folien und gestrichene Papiere. Versuche mit Faltschachtelkarton ist der nächste Schritt, wobei man hier keine speziellen Probleme sieht. Es fehlen noch der Einsatz mit hohen Auflagen und der tägliche Produktionseinsatz über einen längeren Zeitraum in einer Druckerei.
Das einzige noch gelegentlich auftauchende Problem – dessen Ursprung noch nicht ganz geklärt ist – sind die Markierungen beim Druckbeginn auf dem nachfolgenden Druck. Hier habe sich klar gezeigt, dass Platten mit flachen Punktoberflächen und mit einer Oberflächenrasterung eine optimale Lösung des Problems sind. Insgesamt ist die Druckqualität sehr gut und konstant, ein offener scharfer Druck. Inwieweit Verläufe ins absolute Papierweiß in Zukunft möglich sind – wie im Offset oder Tiefdruck – muss sich noch zeigen. Der Druck mit diesen Niedrigreliefplatten sollte auf jeder neuen modernen Flexodruckmaschine der führenden Hersteller ohne Weiteres möglich sein.
Bleibt die Frage: Worauf warten wir eigentlich noch? Dass Planoflex funktioniert, scheint bewiesen. Teurer wird das Verfahren nicht und erfordert keine neuen Investitionen. Schreiben Sie Ihre Meinung an helmut.mathes@alice.it oder klos-geiger@labelpack.de (Fotos / Grafik: Dreher / DFTA-TZ)