Die Standardisierung von Rasterwalzen-Spezifikationen verfolgt das Ziel der Kostensenkung und verbessert gleichzeitig die Druckqualität. Wie sich das in die Praxis umsetzen lässt, zeigte die Zecher GmbH in einer Vortragsreihe, zu der 150 Teilnehmer aus der Verpackungsindustrie und Beschichtungstechnik Ende Januar nach Stuttgart kamen. Im exklusiven Ambiente des Mercedes-Benz Museums kam auch der Spaß nicht zu kurz. Dafür sorgte ein eigens engagierter Wortakrobat. Für ihn war klar, die Zeche bezahlt Zecher. – Ein Bericht von Dieter Finna, pack.consult
Eine oftmals an Zecher gerichtete Frage lautet: »Was gibt‘s Neues bei Rasterwalzen?« Neben Produktneuheiten sicherlich auch einen exklusiven Service oder hohen Kundennutzen. Die Möglichkeiten, effektiver und kostengünstiger zu arbeiten, standen darum im Mittelpunkt des internationalen Kundenevents »Save The Date To Save Your Money«. Thomas Reinking, Sales und Marketing Director und Rüdiger Wand, Managing Director begrüßten die Gäste im Mercedes-Benz Museum, das mit Automobiltechnik aus mehreren Jahrhunderten einen attraktiven Rahmen für die Kundenveranstaltung bot.
Ganz im Mittelpunkt standen die Präsentationen des vertrieblichen und technischen Service-Teams von Zecher, die die vielfältigen Möglichkeiten für Einsparungen durch Prozess- und Kostenoptimierung bei Rasterwalzen vorstellten. Armin Hiltl und Sven Krüger (beide Area Sales Manager) zeigten verschiedene Möglichkeiten auf, über die Spezifikationen von Rasterwalzen Kosten zu sparen. Welche Parameter die hohe Qualität der Zecher Rasterwalzen bestimmen und welchen Service Zecher bietet, fassten André Huber (Key Account Manager) und Holger Nenstiel (Area Sales Manager) zusammen. Und natürlich wurden auch Highlights aus technischer Sicht präsentiert. Jörg Rohde (Head of Application Technology), fasste die Rasterwalzen Entwicklung im Flexodruck zusammen und gab einen Überblick über den neuesten Stand der Gravur-Technologie.
Effektiveres Arbeiten um Geld zu sparen
Was Zecher unter Prozessoptimierung für seine Kunden versteht, zeigten Armin Hiltl und Sven Krüger auf. Prozessoptimierung führt über den Schritt der Rasterwalzen-Standardisierung zu einer Kostenoptimierung. Sie zeigt sich
- in einem reduzierten Rasterwalzenbestand,
- führt zur Einsparung von Farbkosten,
- verringert Rasterwalzenwechsel und Rüstzeiten,
- ermöglicht eine höhere Maschinenverfügbarkeit,
- und verringert den Handlingsaufwand von Rasterwalzen und damit die Gefahr von Beschädigungen.

Rasterwalzenbestände sind in vielen Betrieben oftmals historisch gewachsen, teilweise als Mix unterschiedlicher Hersteller. Ausgangspunkt für eine Standardisierung der Bestände sind die Zecher Spezifikationspyramiden und die zu Grunde liegenden ausführlichen Spezifikationstabellen. Sie zeigen eine Abstufung in den Lineaturen von 60 L/cm für den Rasterdruck, da kleinere Abstände in den Lineaturen bei Rasterwalzen keinen Sinn machen – eine Erkenntnis, die aus umfangreichen Drucktests hervorgegangen ist.
Reduzierung der Farbkosten
Das Einsparungspotential an Druckfarbe wurde am Beispiel des Übertragungsverhaltens einer H.I.T Rasterwalze mit 140 L/cm und 17 cm3/m2 gegenüber einer bislang eingesetzten Flächenwalze mit 60 L/cm Hex 60° Gravur und 19 cm3/m2 aufgezeigt. Die Gravurtechnologie H.I.T. reduziert die Steganteile und führt zu einer verbesserten Farbübertragung bei Flächen.
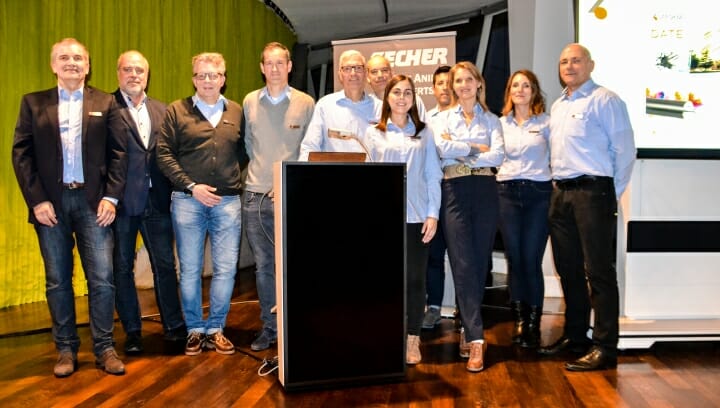
Durch die bessere Farbdeckung konnte in einem repräsentativen Praxisbeispiel der Farbverbrauch um 20% verringert werden, bei gleicher Opazität und dem Vorteil von weniger Pinholing und homogenerem Ausdruckverhalten. Auf eine jährliche Laufleistung einer Druckmaschine von 50 Mio. Laufmetern gerechnet, ergibt sich bei einer Flächendeckung von 60% und einem Farbpreis von 3,50 EUR/kg eine Kostenersparnis bei Weiß von mehr als 100.000 EUR/Jahr.
Standardisierung einer bestehenden Rasterwalzenstruktur
Wie ein gewachsener Rasterwalzenbestand von 30 Walzen in zwei Standardisierungsschritten abgespeckt werden kann, wurde an einem Praxisbeispiel veranschaulicht. Mit der Umstellung auf Hex 60°- und H.I.T.-Gravuren kann die Anzahl an Spezifikationen halbiert werden. Konkret werden 8 Rasterwalzen weniger benötigt, die Bestandskosten sinken in diesem ersten Schritt um 23%. In einem zweiten Schritt, wenn überwiegend SteppedHex-Gravuren eingesetzt werden, kann eine weitere Rasterwalze eingespart und die Bestandskosten nochmals um 5% gesenkt werden.
Die Vorteile der SteppedHex-Gravur liegen in der besseren Farbübertragung verbundener Zellen und dies bei allen Druckgeschwindigkeiten. SteppedHex-Walzen sind kompatibel mit allen Farbsystemen, zudem wird der Farbtransfer durch die verlängerten Zellen homogener. Ein weiterer Vorteil liegt im besseren Reinigungsverhalten durch die größeren Zellöffnungen.
Kostenoptimierung durch Standardisierung bei Christiansen Print
Über die praktische Umsetzung des Projekts Standardisierung/Kostenoptimierung bei Christiansen Print berichteten Björn und Sascha Vorlop im Gespräch mit Jörg Rohde. Sascha Vorlop ist Druckereileiter bei Christiansen Print, Björn Vorlop kümmert sich als Betriebsingenieur auch um zahlreiche Projekte. Ausgangspunkt bei Christiansen Print war eine fundierte Datenanalyse im Lean Management, bei der festgestellt wurde, dass hohe Rüstzeiten ihre Ursachen in vielen Rasterwalzenwechseln hatten. Zum Bestand zählten 34 Rasterwalzen zweier verschiedener Hersteller, die sich bei gleicher technischer Spezifikation teilweise im Ausdruckverhalten unterschieden. Anlass genug, einen Standard zu finden, der die Rüstzeiten reduziert und den Nutzungsgrad der Maschinen erhöht. Der Ist-Zustand zeigte 30 Rasterwalzenwechsel am Tag, mit dem Ziel, diese um 50% zu reduzieren.
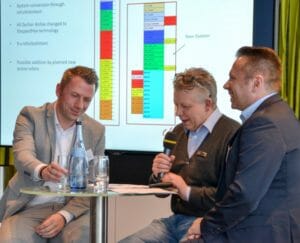
Für das eingesetzte Projektteam stellte sich im Laufe des Verbesserungsprojektes eine 460er SteppedHex mit 5,5 cm3/m2 Schöpfvolumen als die geeignete Rasterwalzen Spezifikation heraus. Mit ausschlaggebend war, dass keine Anpassung in der Repro benötigt wurde. Unter Berücksichtigung bestehender Jobs war dies ein entscheidendes Kriterium.
Die Implementierung bei Christiansen Print erfolgte schrittweise, indem bestehende Rasterwalzen turnusmäßig auf SteppedHex überarbeitet wurden, so dass keine zusätzlichen Kosten entstanden. Positiver Nebeneffekt nach der Umstellung waren weniger Beschädigungen, da weniger Walzen transportiert wurden. Die Anzahl der Rasterwalzenwechsel konnte von 30 auf 5 pro Tag gesenkt werden. Eine Analyse des Farbverbrauchs der SteppedHex Walzen ergab, dass in dem Analyse-Zeitraum von 16 Monaten eine Einsparung von 10% Farbe erzielt wurde. Die Farbstärke musste über Verschnitt-Zugabe einmalig angepasst werden.
Qualität und Service
Durch die zentrale Produktion in Paderborn erhalten Kunden stets die gleich hohe Qualität auf demselben Niveau, egal wo auf der Welt die Kunden die Produkte einsetzen. Dies stellten André Huber und Holger Nenstiel nochmals heraus. Die Prozesse dafür sind zertifiziert, geprüft und reproduzierbar. Zecher greift bei Forschungs- und Entwicklungsthemen auf eine eigene R&D zurück. Dort werden auch anwendungstechnische Themen behandelt, teilweise auch Reklamationen ergründet.
Das Thema Reinigung von Rasterwalzen ist zum Prio-Thema geworden, auf das Thomas Reinking abschießend einging. Die Frage, was das richtige Reinigungsverfahren ist, um eine perfekte Reinigung einer Rasterwalze zu gewährleisten, lässt sich nicht pauschal beantworten. Zecher hat sich auf die Fahne geschrieben, in jedem Reinigungsverfahren zu Hause zu sein, um die Auswirkungen auf die Rasterwalzen zu kennen. Mit diesem Know How bietet Zecher die kompetente Unterstützung bei allen Fragen zur Reinigung der Rasterwalzen für seine Kunden an.
Zecher GmbH
Der internationale Hersteller von Rasterwalzen aus Chrom und Keramik wurde 1948 von Kurt Zecher gegründet. 1950 fertigte das Unternehmen die weltweit erste regelmäßig gravierte Rasterwalze. Mit kontinuierlichen Weiterentwicklungen und drucktechnischen Innovationen kann die Zecher GmbH heute auf eine über 70-jährige Erfahrung in der Rasterwalzenfertigung zurückblicken. Am Firmensitz in Paderborn fertigt das Unternehmen mit über 170 Mitarbeitern in vier Produktionswerken jährlich rund 12.000 gravierte Rasterwalzen, davon ca. 10.000 Keramikwalzen. Zecher-Rasterwalzen werden in Druckmaschinen auf der ganzen Welt eingesetzt, im Etikettendruck, der flexiblen Verpackung, im Offsetdruck, in der Beschichtung und im Wellpappen Pre- und Post-Print. Sie werden über ein kontinuierlich wachsendes Netzwerk aus Vertriebspartnern in 70 Ländern vertrieben.
〉 www.zecher.com
Stimmen zur Veranstaltung
»Als Einsteiger in den Flexodruck ist das Thema Rasterwalzen-Standardisierung für uns super interessant.« (Peter Schultheiß, Head of Production bei Töpfer Kulmbach GmbH)
»Wir sehen uns in unseren Bemühungen zur Rüstzeitoptimierung bestärkt. Jetzt wollen wir das im Wellpappendruck testen und die Anzahl an Rasterwalzen reduzieren, sowie Kosten zu senken.« (Alfred Harlas, Betriebsleiter Klingele Papierwerke Hilpoltstein)
»Besonders interessiert haben mich die SteppedHex Rasterwalzen mit geringerem Farbverbrauch und flexiblerem Einsatz.« (Jürgen Scherm, Druckvorbereitung Fr. Schiettinger KG)
»Es war ein super Seminar mit sehr informativen Inhalten. Die Lokation war spitzenmäßig und für jeden war etwas dabei.« (Carsten Gärtner, Projektleitung Drucktechnik, Palm Verpackung)