Dieter Finna · pack-consult.org · (For a German version click here).
Multilayer labels are true communication gems. Their multi-layered structure provides plenty of space for comprehensive information without overloading the label design. But what high-precision machine technology is behind the production of these space-saving wonders? The Gallus Labelmaster demonstrates the perfect interplay of efficiency, precision and flexibility in multi-web label production.
Multilayer labels are characterized by an immense amount of space in a very small area. Also known as peel-off labels, they enable highly efficient communication for retailers, which they increasingly need to meet constantly growing information requirements.
Problem solvers in the market segments
Multilayer labels are firmly established in all market segments. In the pharmaceutical sector, they can be found on folding cartons, vials, cans and blister wallets, where they are used to clearly communicate dosage instructions, warnings and information on ingredients. In the food sector, they enable precise labeling of copious ingredients and additives, origin information and allergens. For multilingual versions in particular, multi-layer labels provide the necessary space to concisely convey information in all language variants.
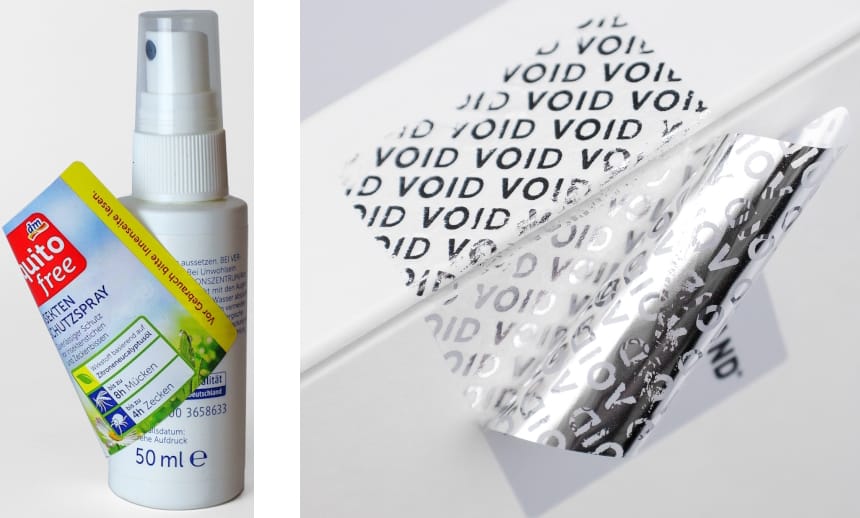
On household product packaging, they convey important warning and handling instructions. In the security sector, they are used as void labels, where any attempt to remove the label irreversibly separates the film and adhesive, revealing a void message or pattern as clear evidence of tampering. In logistics and e-commerce, they facilitate product tracking and returns management, and hardly a day goes by without new applications being added.
Production process with sophisticated web guidance
The easiest way to explain the differences in the production process of multi-layer labels is to look at them from the substrate side. A common production method is based on a single substrate web. First, the reverse side of the substrate is printed, followed by the front, before the web is slit into narrower webs. These are then configured on top of each other to create a multilayer label. In this example, the result is a three-layer label with five printed sides. However, the maximum label width is limited to approximately one-third of the original web width.
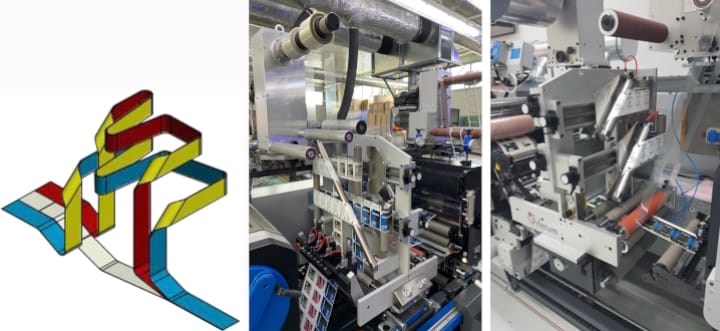
The manufacturing process differs when using a machine with multiple unwinders, where production is carried out with several substrate webs. This method allows for the use of different printing materials and enables high-volume production.
Modular printing presses can be equipped with up to three unwinders and often feature 12 or more inline printing units. Additionally, a rail system above the printing units can accommodate applications such as cold or hot foil stamping, providing further options for unwinding and rewinding.

In multi-web applications, precise web transport is crucial. Only with utmost precision can different substrates such as polypropylene, polyethylene and paper webs be accurately combined to form a single label. This is achieved through a highly precise machine control system, which adjusts the unwinding and web tension of the materials according to their respective E-modulus — a crucial factor, as the stretch properties of these materials vary greatly.
With register control in the longitudinal and traverse alignment, one web is defined as the master, while the other webs are synchronized to it. This ensures that all webs are perfectly aligned, enabling precise and stable further processing.
System to Compose
If existing Gallus Labelmaster press systems are to be expanded for multi-web label production, the »System to Compose« offers the necessary options with its modular design. Each machine system can be upgraded with flexographic and screen-printing units, for example, to enable reverse printing as the first production step, as well as for haptic effects or the application of braille lettering.
Adding a digital printing unit allows for variable data printing in one to four colors, with an optional color gamut expansion including orange and violet. Additionally, die-cutting units can be retrofitted, which are often required between printing units in multi-web applications.


From Roll to Multilayer Label
The production of multilayer labels differs from that of traditional pressure-sensitive labels (PSL) right from the unwinding of the roll material. The printing sequence often begins with reverse printing. For this, the web is unwound with the liner facing up, the substrate and liner are separated, and the open adhesive back is printed in the first flexographic printing unit, as shown in the sample label »Body Sport«. Subsequently, both layers are recombined, pressed together, and the web is turned over for printing on the front. The four-color design is then printed in four flexographic printing units (CMYK).
The next finishing step is a cold foil transfer and, most importantly, the neutralization of the adhesive on the backside. Various processes are available for this, such as release varnish or glue killer. In this case, a release varnish is applied to the front so that the individual sides of the multi-layer label can be opened without any problems.
In the next step, haptic effects are applied in a screen-printing unit before the webs are cut and precisely superimposed to form the multi-layer label.
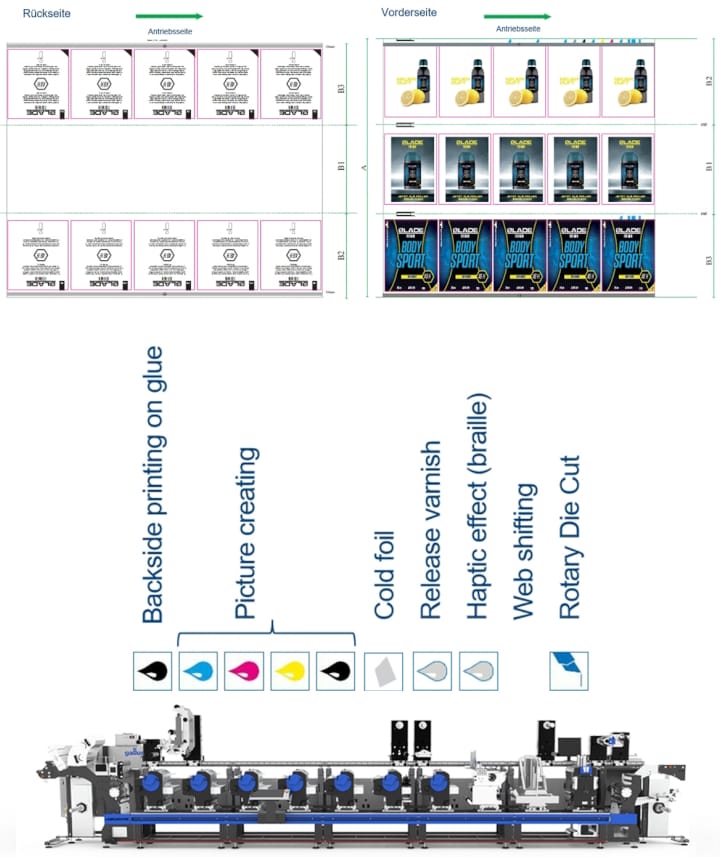
Process variability is crucial in day-to-day business
This example label illustrates the high demands that the production of multi-layer labels places on the machine configuration. Fast and flexible changeover of the machine system is a crucial factor for efficient production. Since multi-layer label designs require very different processing sequences, flexo and screen-printing units, as well as die-cutting units must be able to be placed at different positions in the machine, depending on the job. Where one job might require a screen- printing unit in the machine sequence, the next one might require a die-cutting unit in that position. Efficiency in production is therefore achieved by ensuring that modules can be exchanged easily, quickly and flexibly.
Intuitive Control
Other features crucial for efficient multi-layer label production include easy operation and control of the machine via the HMI (Human Machine Interface). Especially with longer machines, the system supports the operator by providing real-time information on the status of the printing units, register accuracy, and the processes on the rail above the printing units at all times. This includes parameters such as tension or the status of web tension units and web edge guides – regardless of the operator’s location at the machine.
Machine Concept with Minimal Waste and a Stable Production Process
Especially in the production of multi-layer labels with long web paths, waste plays a key role in effective and sustainable production. With the Gallus Labelmaster, this aspect is optimized with a short web path of just 1.4 m between the printing units and a compact arrangement of all key processes on the primary level. This eliminates additional web paths of 4–6 meters that would arise when changing to other machine levels. This reduces waste, saves time and cuts costs, especially with frequent job changes.
At the same time, short web paths lead to a high level of stability in the production process, which optimizes the use of materials in multi-layer labelling, as well as ensuring simple operation and high efficiency.